Laser pipe – also known as laser tube – is an important machine for tube production. The very latest and most advanced pipe laser machines also enable 3D tube processing – i.e. three-dimensional processing on straight tube blanks. For this reason, 3D pipe (tube) lasering forms an integral part of the techniques and methods used for bending and rolling tubes of any shape, and made from any metal alloy.
With the introduction of tube lasering, tube processing is now possible that would have been unthinkable a few decades ago.
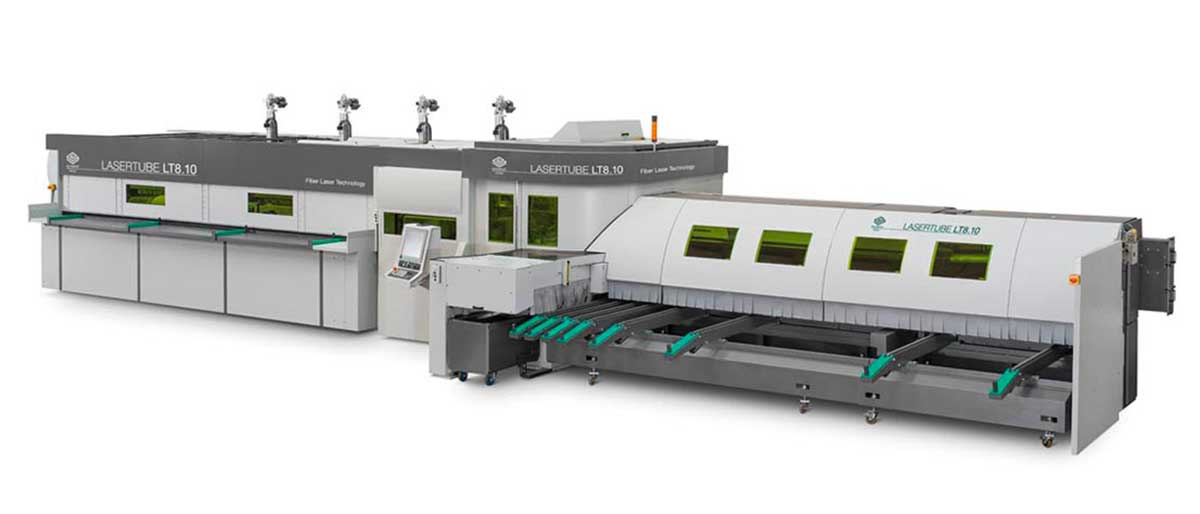
What is laser pipe? What does pipe lasering means?
Pipe or tube lasering is a tube processing method that allows tubes to be cut and processed by the targeted application of light beams concentrated by the emission of electromagnetic radiation. Tube laser cutting is carried out by a specialised machine – the laser pipe machine, also called Laser Tube.
Laser technology has revolutionised the world of metal tube processing by leaps and bounds. It was Albert Einstein who laid the theoretical foundations of the modern tube laser at the beginning of the twentieth century by explaining the phenomenon of ‘stimulated emission’, which remains the physical basis of all lasers to this very day.
The first machines capable of cutting metals with laser-based systems were first produced in the 1960s, however. After explaining the background to laser tube machines, we now want to see how they actually work.
How does tube laser cutting work?
Laser pipe uses a focused beam of high-power electromagnetic radiation that heats the metal tube to a temperature where it melts and vaporises. Nor is tube laser cutting restricted merely to cutting through metal tubes. Tube lasers can also be used in many other types of tube processing involving bending and rolling (roll bending), such as:
- Drilling work
- Tube slotting
- Mitre cuts across the tube width
- Lettering engraving
- Tube marking
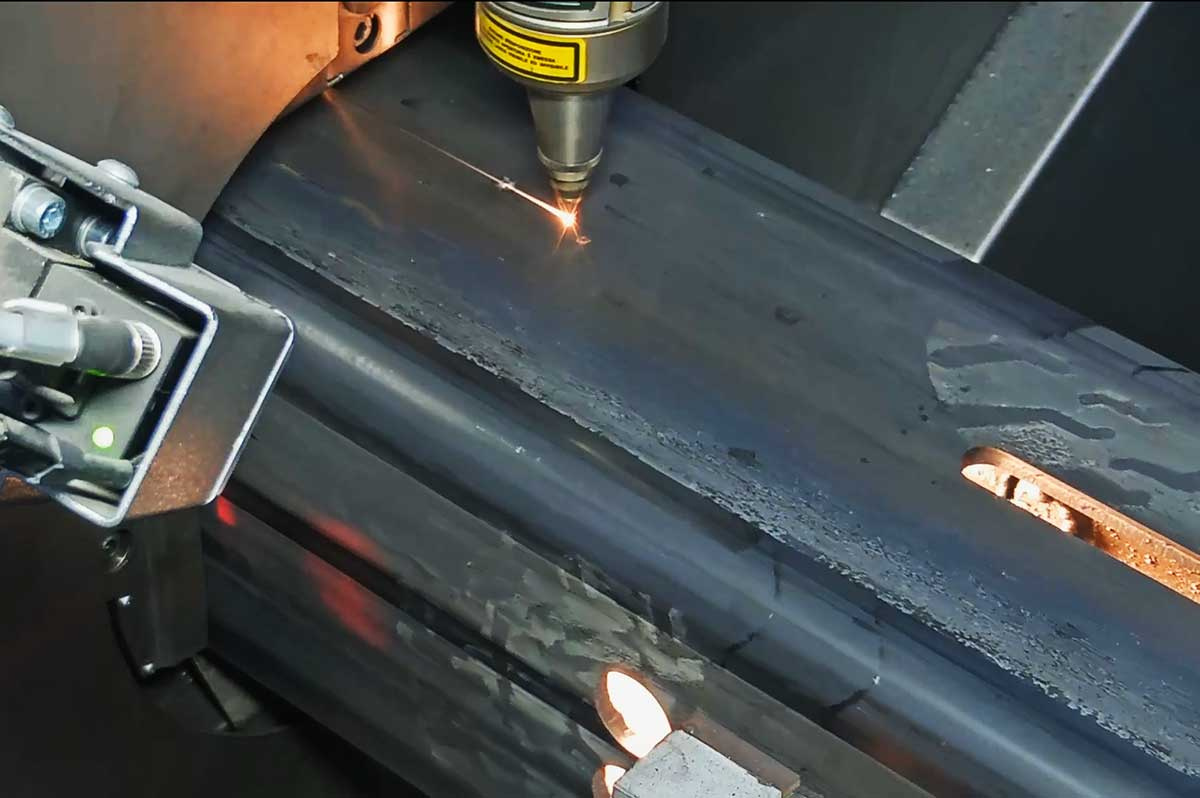
Tube cross-sections and metals that can be processed by laser tube cutting machines
Tube cross-sections
In contrast to conventional tube cutting machines, laser tube machines can process tubes with much larger cross-sections. Modern CNC-based laser tube cutting systems are suitable for cutting and processing tubes of any shape:
- Round tubes
- Square/rectangular tubes
- Oval and elliptical tubes
- Hollow sections
One special application for laser tube machines is the processing of structural sections (also known as hollow sections). Unlike tubes and pipes, which have a round or square/rectangular cross-section, these sections can have all kinds of different geometric shapes and are typically manufactured for use in a very wide range of applications. Just a few examples of these applications include:
- Construction of cabs for earth-moving machines
- Lighting systems
- Door or window frames
With a laser tube cutting machine, you can cut any cross-section and any geometric shape of structural section without needing to set up any special kind of tooling.
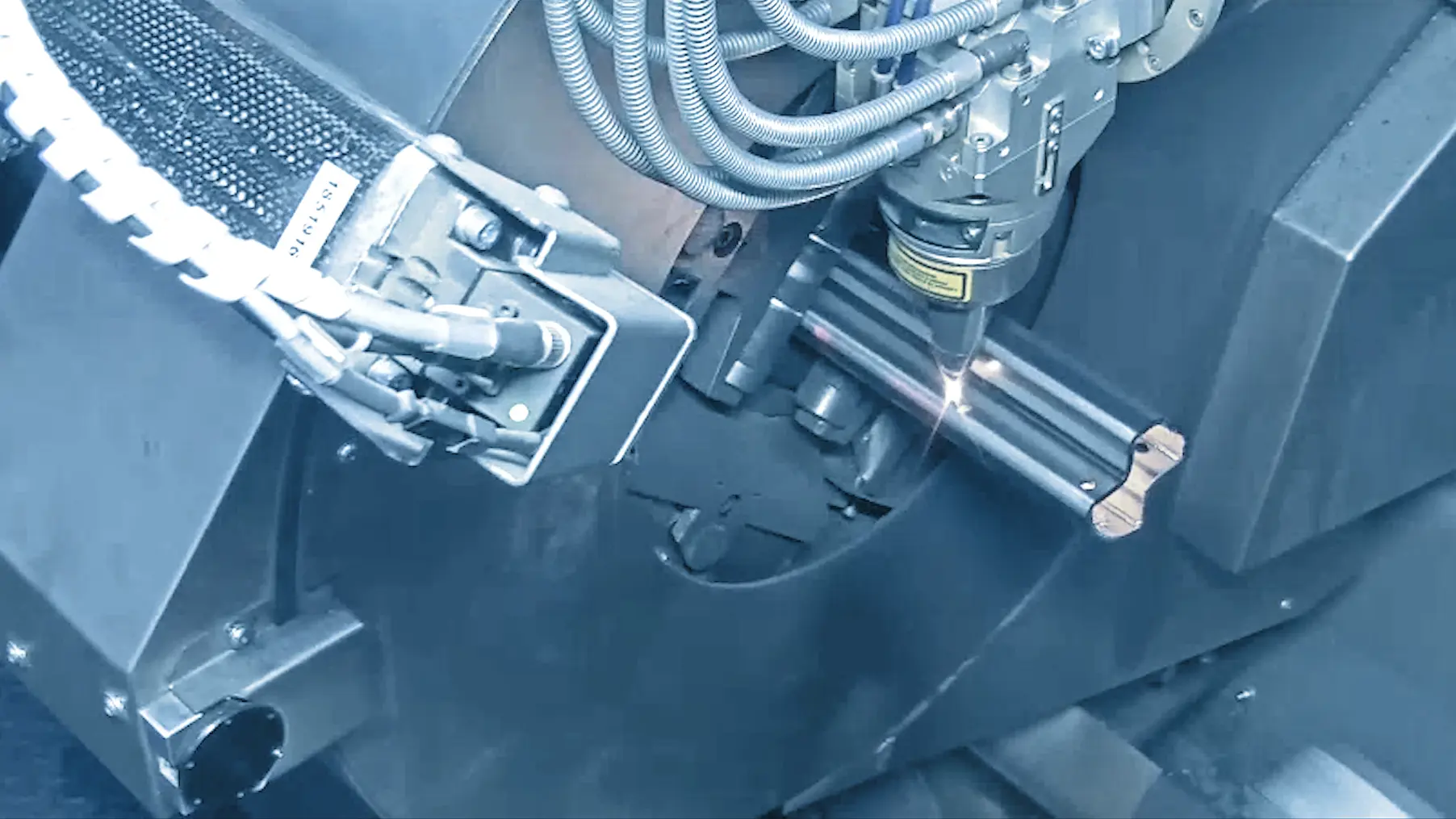
Metal alloys
Tube laser cutting is used to cut tubes made from any of the standard types of metal alloys:
- Steel tubes – used in the construction of agricultural machines as well as in the general construction industry
- Stainless steel tubes – used for the construction of systems used in industry and heating, and in food production plant and heat exchangers
- Aluminium tubes – used for making furniture and lighting systems. Also used in the fit-out of subways, rail carriages, buses and cars (windows, handrails, etc.).
Twin loader for greater production efficiency
Modern tube lasers feature two loaders. One of these is used to feed in tube or structural sections with a length of over 6 metres (up to 12 metres). The other is used to load tubes up to six metres in length. This makes it possible to cut a series of tubes with the laser while simultaneously also queueing up the tubes for the next job.
Depending on the length of the tube, modern tube lasers also feature unloading mechanisms that enable the simultaneous processing of tubes of different lengths.
Oxygen and nitrogen: assist gases for laser cutting
To ensure that a laser cut – which is created as a result of a material being melted by a laser beam – is as clean as possible, certain types of gas (also known as ‘assist gases’) are used. These assist gases help to remove the residues and impurities caused by the melting process.
The following reactive and non-reactive gases are used for laser cutting:
- O2 – oxygen
- N2 – nitrogen
What are the differences?
The first difference between these two gases is their cost. In general, laser cutting with nitrogen costs more than laser cutting with oxygen. There are also a number of other aspects that need to be considered when choosing nitrogen or oxygen as the assist gas for laser cutting:
- Tube diameter
- Need for a clean laser cut
- Speed of the cutting process
In terms of the diameter, oxygen enables even heavy-duty steel tubes – up to 15 mm thick – to be cut with the laser if greater performance is required to do so. Nitrogen is used for the laser cutting of thinner steel, stainless steel and aluminium tubes.
A table summarising the diameters that can be processed by the new laser tube machines from Tecnocurve is presented below, listing the gas and material used, and the type of processing that is possible. The table covers both 2D and 3D tube processing.
O2 STEEL | N2 INOX | N2 STEEL | N2 ALUMINIUM | |
2D | 15 mm | 6 mm | 6 mm | 6 mm |
3D up to 30° | 10 mm | 4 mm | 4 mm | 4 mm |
3D up to 45° | 8 mm | 3 mm | 3 mm | 3 mm |
The need for a clean cut is another key aspect to consider when choosing the right assist gas for tube laser cutting. Laser cutting with oxygen does leave oxide residues, for example. These residues are especially visible if the laser-cut tube is then painted or (as is often the case for steel tubes) is galvanised after the tube bending stage. Using nitrogen as an assist gas results in a clean cut with no oxide edge.
Lastly, nitrogen laser cutting enables higher processing speeds to be achieved than laser cutting with oxygen.
Laser tube with tube bending and tube rolling
Completing tube processing work before bending and/or rolling (roll bending) means that the tube processing phases can be eliminated, along with the resulting extra costs that these produce in terms of retooling other machines.
This is where the precision tube bending company Tecnocurve saves you money. We can complete these kinds of cuts with tube lasering before tube bending:
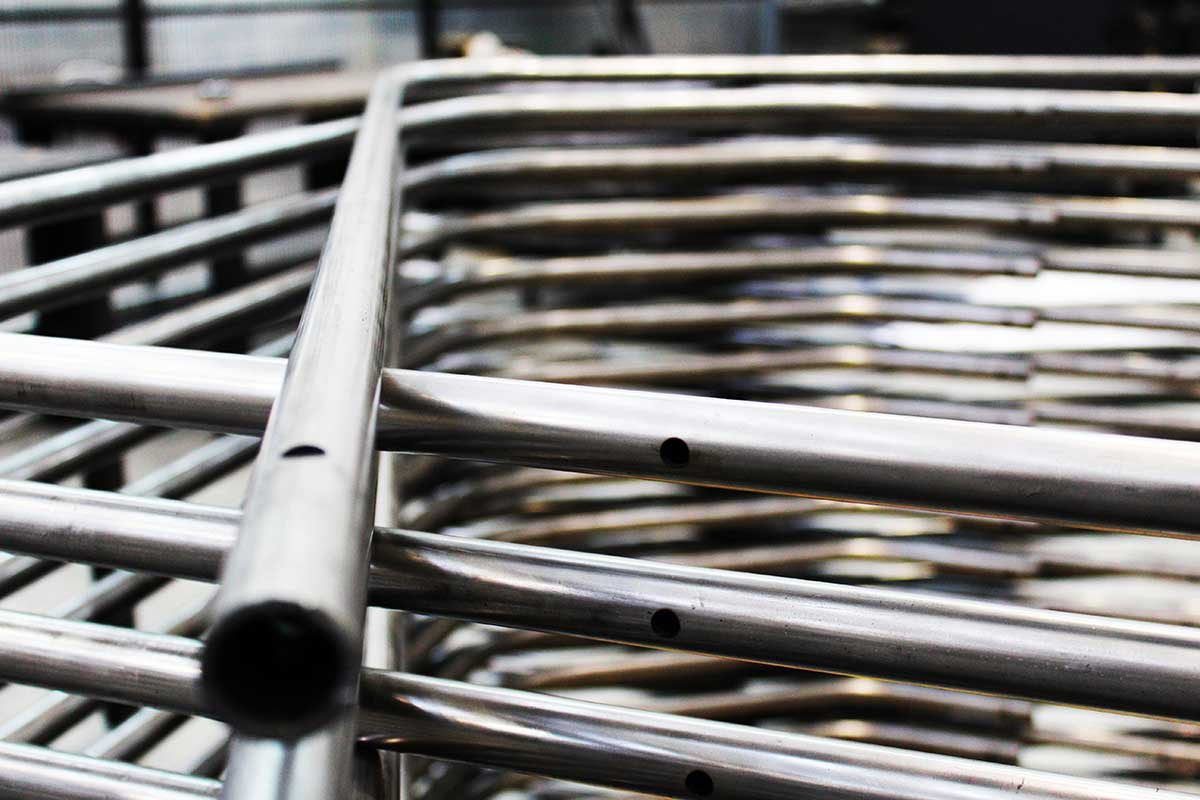
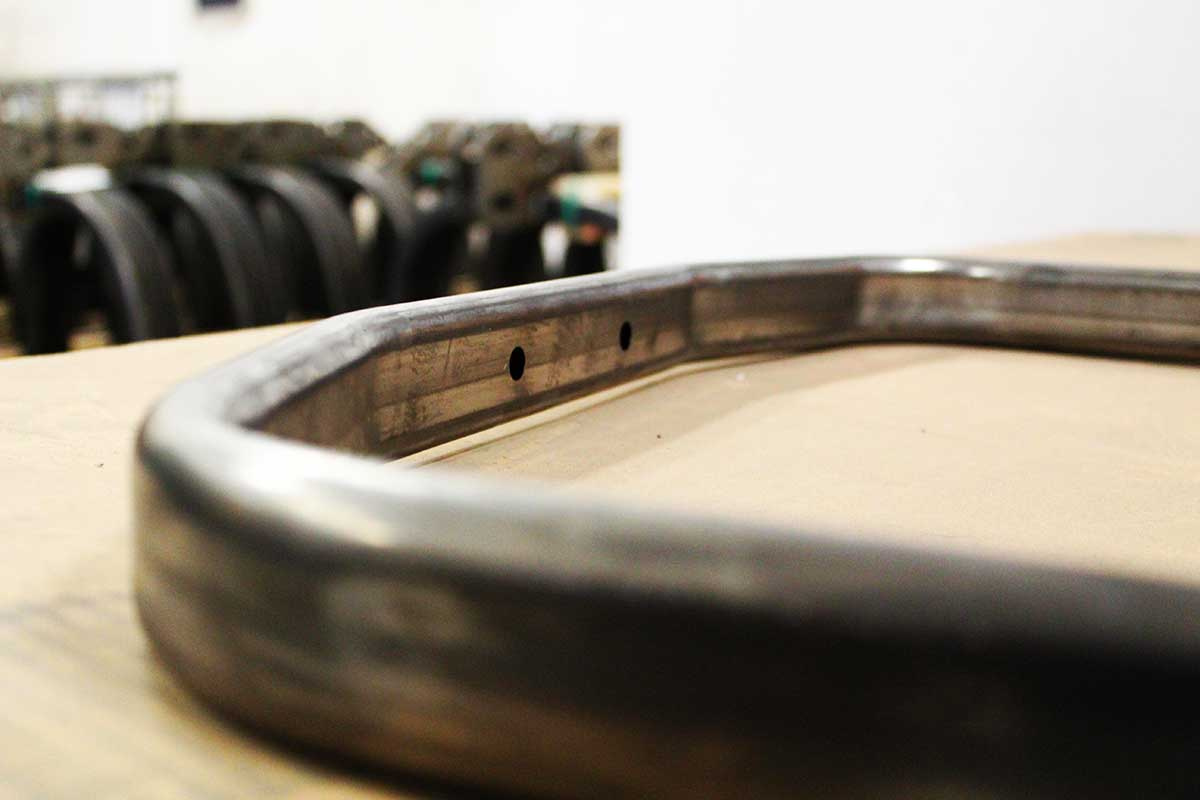
Laser pipe drilling
Countersunk holes – which are generally used as the seat for fixing screws – can be punched before cold forming. However, this is possible only if the laser tube machine can be angled on the tube. The laser tube machine in our machine pool can be tilted by up to 45°, for example.
Mitre cuts across the tube width
The tube laser enables mitre cuts to be made across the entire tube width without the cut being interrupted by the thickness of the tube wall – as can be clearly seen in the drawing shown below.
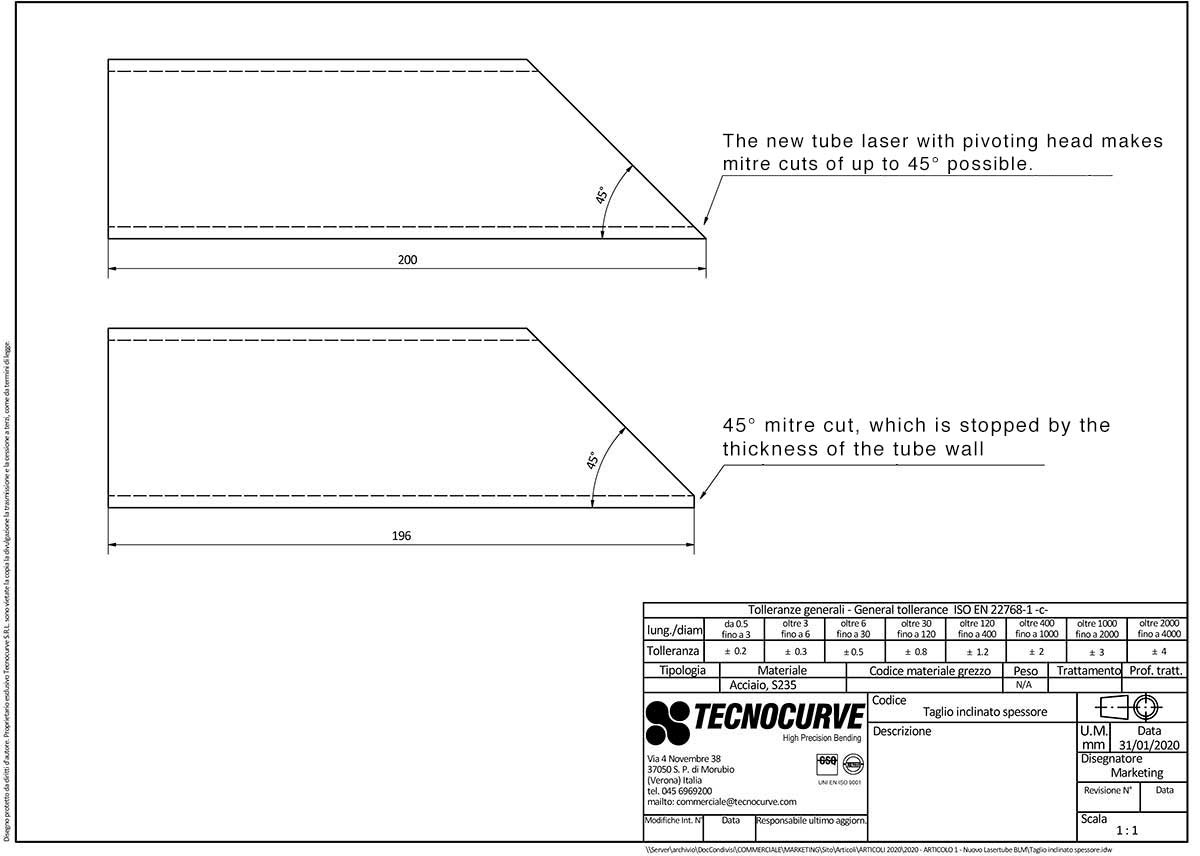
Laser cutting and 3D software: a successful combination
- 3D simulation of laser cuts, so as to solve any problems before starting tube processing
- Processing notes to help the operator of the tube laser
- Fully-automated calibration
- Creation of a list of cuts that guarantees minimal waste, so as to optimise the production cycle
- Creation of a report on cutting results (processing time, number of units, scrap)
- Cutting cycle logging – enables the actual duration of the cutting operation to be checked later
- Support for laser-cut ‘locking tube connections’
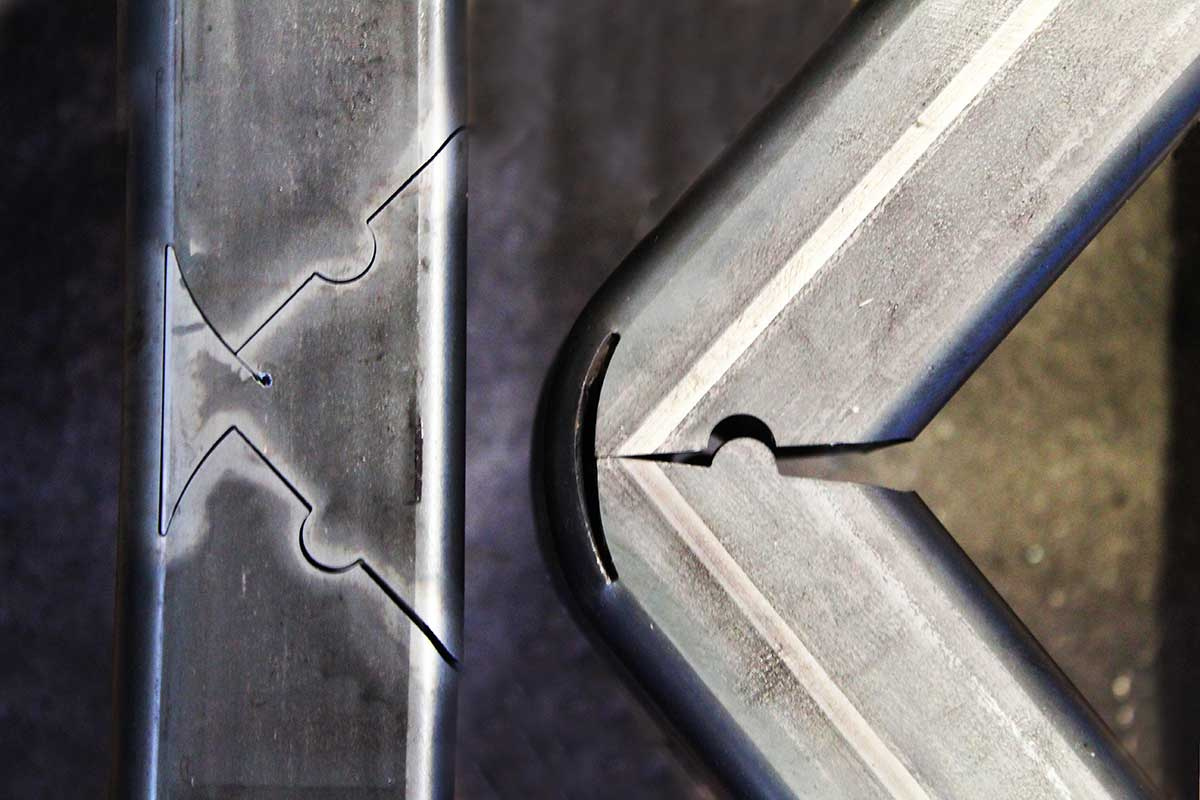
- Handling of special tube processing methods
- Correction of defects resulting from straightness errors in material blanks
- Maggiore affidabilità in caso di variazione dello spessore del tubo
- Detection of tube welds and automatic cut correction: the software adjusts the cutting power output to the thickness of the weld seam
Conclusions
The tube laser is an ultramodern machine that has revolutionised tube processing methods – and tube bending and tube rolling in particular. Tube lasering enables the acceleration and optimisation of the production cycle.
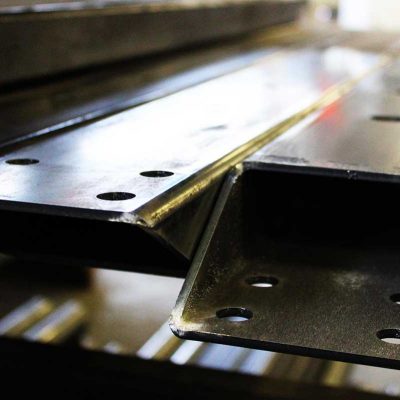
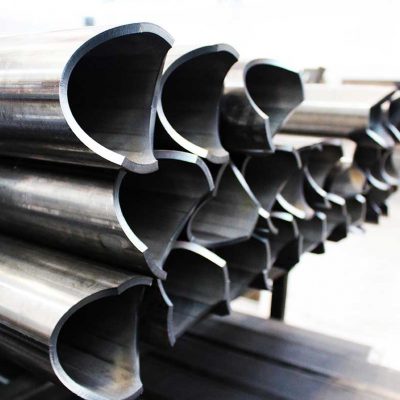
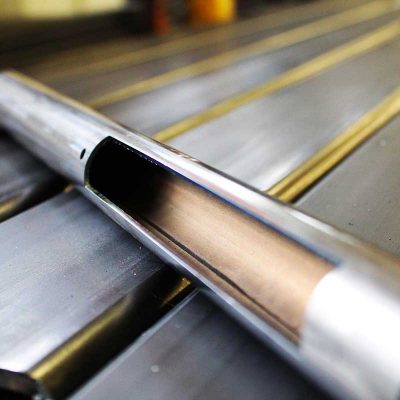