Welding, laser cutting, bending and roll bending are perhaps the most important processes carried out on metal tubes. In a previous article we examined the question of the relationship between bending and welding of steel tubes, focusing mainly on the risks and costs of welding.
The main problems connected with welding the tube have to do with the fact that it alters the mechanical characteristics of the metal. In addition to this, the esthetic appearance of a bent tube is appreciably better than that of a welded one.
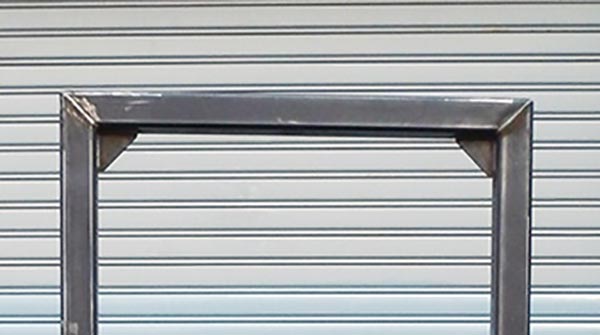
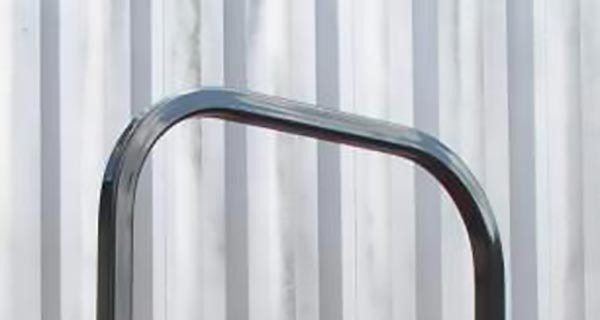
Welding metal tubes
The following metal tubes can be welded:
- Steel tubes
- Stainless steel tubes
- Aluminum tubes
- Brass tubes
While welding of steel and stainless steel tubes is more common and, all things considered, easier, welding of aluminum tubes is extremely difficult, due to the fact that the material, which is an exceptional heat conductor, also has a very low melting point and requires that the welders take particular precautions and follow strict procedures. The risk is that a severe deformity of the tube would ruin the process, the tube and consequently the end product.
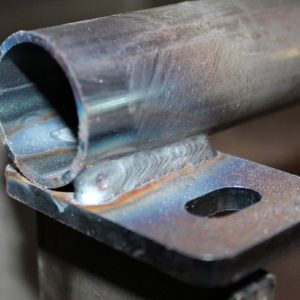
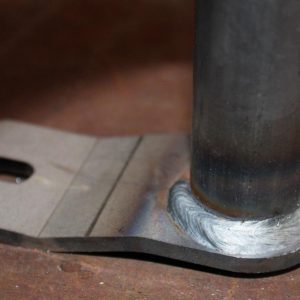
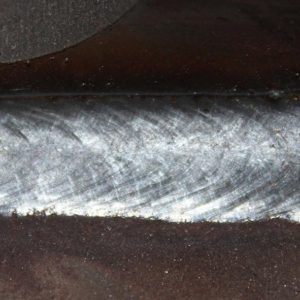
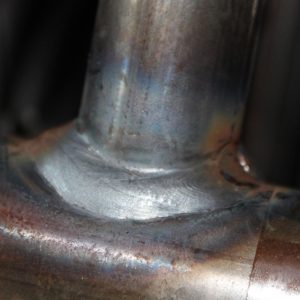
Sectors of application for bent products complete with welding
Tube welding is a process used in a number of industrial sectors. Among these, in particular, is agriculture (for example farm machinery), the automobile industry, lighting, fitness machines, animal husbandry, urban decor and interior design, mechanical systems and, obviously, carpentry.
Type of welding
Metal tubes are welded with two different procedures:
- TIG welding
- MIG/MAG welding
In both cases, protective gasses are used, which serve to insulate the molten material from the atmosphere, ensuring a cleaner joint and, at the same time, better penetration of the weld.
TIG Welding
TIG welding is an arc welding procedure that can be used for metal tubes. It is characterized by a torch on which a tungsten electrode is fitted and which, protected by the gas (Ar – Argon – or He – Helium) melts the parts to be welded. TIG is divided, in turn, into welding with or without filler. The difference lies in the fact that in the former case filler material is added during the melting process. This is done to increase the seal of the weld. It is usually used when joining metals of reduced thickness (from 2 to 5 mm).
This type of TIG welding of metal tubes requires great accuracy on the part of the welder, who must prevent the formation of shards deriving from the electrode, as these could damage or weaken the joint.
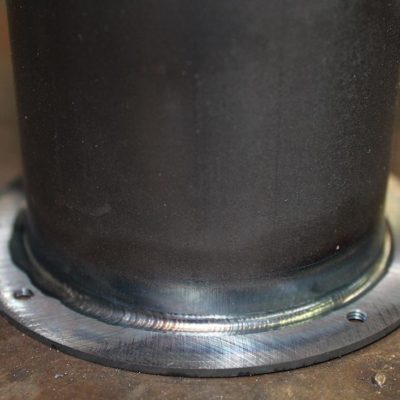
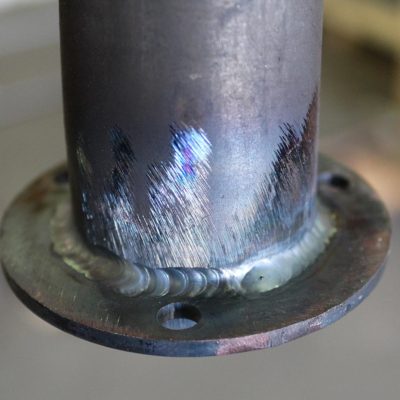
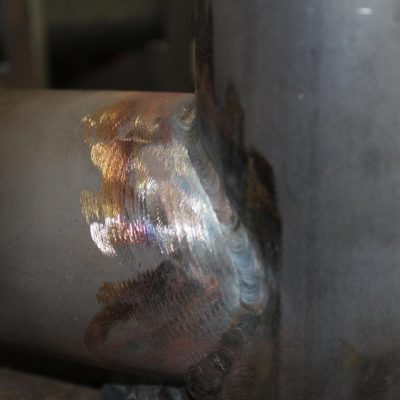
MIG/MAG Welding
MIG/MAG welding – the difference between MIG and MAG consists of the protective gas used – is a continuous wire procedure that ensures high productivity and the elimination of scraps.
Among the advantages, it is possible to achieve greater penetration, which means that fewer “passes” will be needed to fill the joint, and this also makes it easier for the welder to keep the arc under his direct observation, fully controlling the performance of the weld.
This procedure is more rapid that TIG welding and permits great flexibility of use, including the ability to weld very fine thicknesses of tubing.
Among the main problems of MIG/MAG welding of tubes is, first of all, the cost of the welding equipment, which is much higher than that of a machine for TIG welding. Also, cracks may be produced at high heat due to poor cleaning of the edges of the metal to be welded, combined with the presence of pollutants.
Precise regulation of the heat gradient is very important. If it is too high this may result in excessive penetration. If it is too low the two metal parts may not melt sufficiently for welding.
MIG welding on square steel tubes after bending/roll bending in the agricultural sector
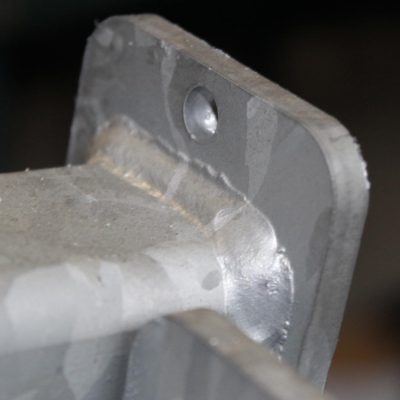
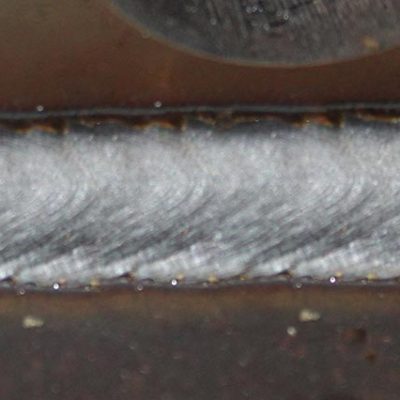
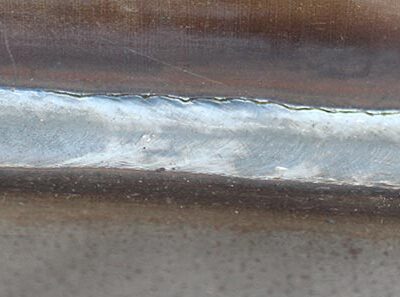
Welding regulations and standards
- ISO 3834 – Requisites of quality for welding by melting of metal materials
- EN 1090 – Certification for steel and aluminum constructions
The welding department at Tecnocurve
All the welders at Tecnocurve have been certified by EsseBi Welding a company specialized in the welding sector.
They have also obtained special qualifications for WPS and WPQR welding procedures.
WPS is a set of data regarding the material used, the protective gas, the welding technique, as well as technical parameters such as position and preheating.
WPQR is the protocol that contains the results of the welding tests. It qualifies the company and/or welder to perform welded joints according to the conditions and parameters established in the standard.
Tecnocurve has five welding stations, spread over an area of about 400 sq.mt. This arrangement allows our welders to work in absolute safety thanks to the aid of the normal equipment for personal protection, the self-obscuring welding masks and a modern exhaust system that operates with low consumption.
These workstations permit welding using either TIG or MIG/MAG procedures.
The quality of our welded tube
Our welding department and the quality control department of Tecnocurve are separate but communicating production zones. This means that quality control can be done immediately on the welded tube.
The welding process actually begins in the technical office. That is where we analyze the drawings and prepare the production sheets containing as much information as possible about the welding process.
Management software allows us to monitor the timing and qualitative outcome of every stage of the tube welding process, to which a process code is assigned.
We also carry out tests with penetrating liquids to ascertain the quality of the tube weld and ensure the absence of cracks. These tests are performed for tubes and metal profiles whose end use requires high welding strength. A typical case is that of pressurized systems.
Lastly, we draft the certification of quality of the weld. The certificate reports on the outcome of the seal test with penetrating liquids and the control measurements we have made. This enables the customer to verify that the welded tube has the requisites specified in the order.
Every detail is welded according to a procedure drawn up during the sampling stage. This serves to ensure that there are no differences among different production lots:
Special sheet metal templates ensure precision welding of the tube
To guarantee the maximum precision of the tubular elements welded, Tecnocurve designs sheet metal templates. These serve to ensure that all the parts are welded in the correct positions. The function of these special templates is illustrated in the figures below.
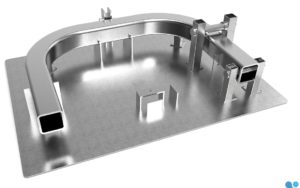
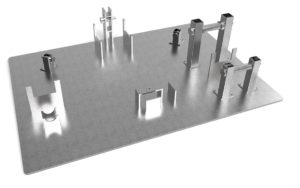
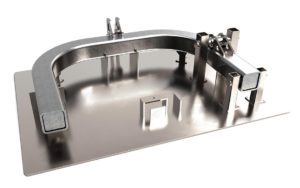
Do you have any questions about tube welding?
Tecnocurve’s experts will be happy to answer them