During the bending process, tubes are subject to tensions that cause deformation of the tube in the bent area. This phenomenon is caused by stretching of the wall in the outside bend and the compression of the wall in the inside bend. (see figure 1).
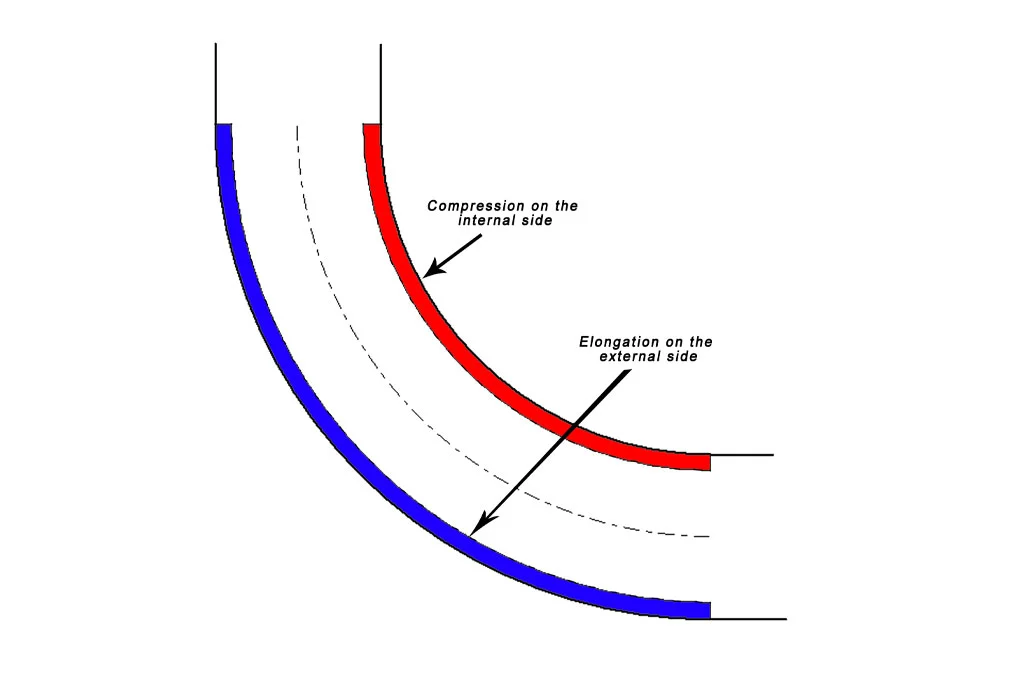
The extent of the deformation varies depending on several factors such as:
- size and shape of the tube (round, square, rectangular or special section)
- wall thickness
- metal type
- bend radius
- bend angle
The increasing need of pre-processing aimed at reducing the cycle times requires an accurate studying of this phenomenon.
A hole made in the vicinity of the bending area before bending the tube will get deformed due to the tensions developed during bending. Such deformation will affect the correct positioning and shape of the hole, leading to significant deviations from the specifications reported in the technical drawing supplied by the customer.
The most widespread solution to overcome this issue consists in bending the tube first and then drilling it in a second step.
This solution allows solving the issue and ensures the necessary drilling accuracy. However, this solution also requires an increased amount of time and resources resulting therefore in an increase of the final tube processing costs.
Thanks to over 25 years of experience in tube and metal profile bending and rolling, the production and technical department of Tecnocurve carried out a laser cutting study that allows us to obtain – by means of Laser-Tubo Trumpf – the outline of the hole before bending the tube. (see figures 2 and 3)
Elliptical hole before bending
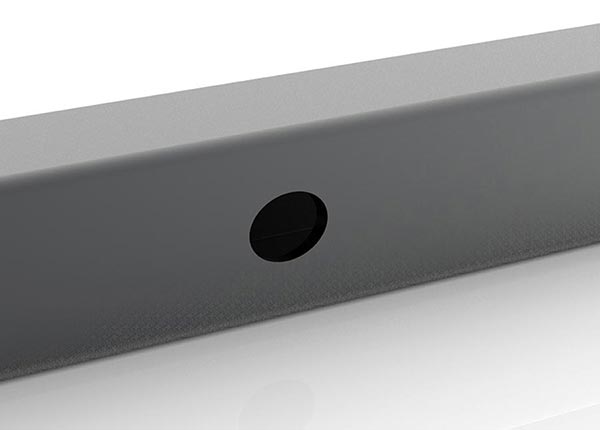
Round hole after bending
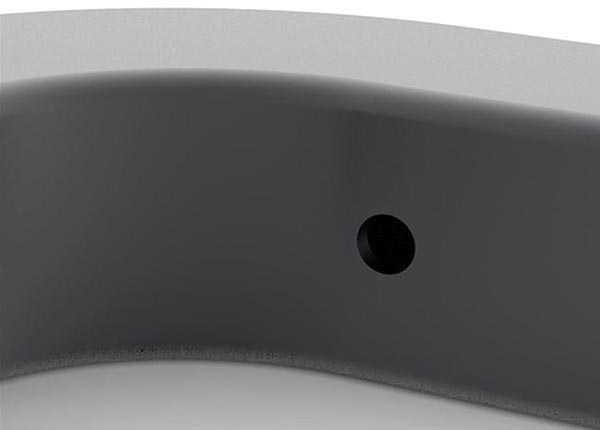
This drilling technique used especially for bending and cutting/drilling steel and stainless steel tubes prevents the aggravation of the production process as a result of a second step for drilling. This allows reducing the production cycle times, decreasing the final tube processing costs.
This special technique can be implemented by means of the latest generation software used by Tecnocurve to analyse the deformation of the tube (deformation that must be constant throughout the entire batch) determining therefore in advance the deformation of the hole after bending.
The result of the analysis allows Tecnocurve to perform a laser pre-cutting of the tube, that will ensure the perfect positioning of the hole on the tube after bending, respecting the technical drawing provided by the customer.
However, pre-cutting is not always possible before bending: the technical department of Tecnocurve must assess from time to time the usability of this technique based on the software analysis results and on the works requested by the customer.
A particularly important factor, for example, is the diameter of the hole that is strictly related to the size of the tube.
In 2016 Tecnocurve also implemented a new process for the realisation not only of round and square holes, but also of laser pre-cutted slots in the vicinity of the bending area. The company’s stated goal is the continuous reduction of production times and costs by carrying out as much works as possible using the Laser Tubo Trumpf before bending.
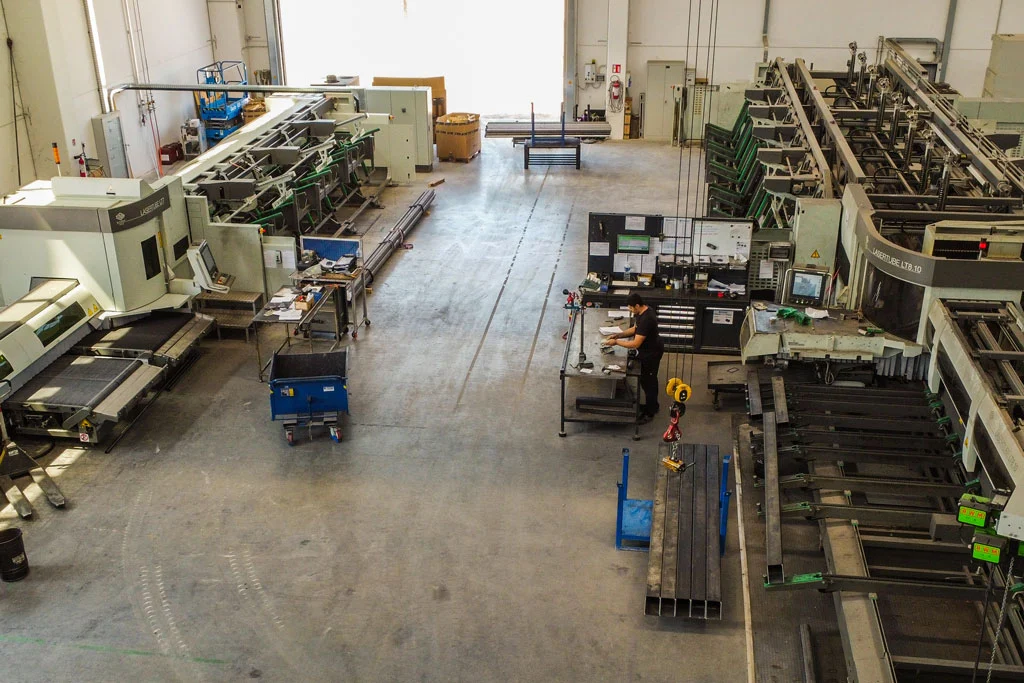