Bending and roll bending of tubes, tubular elements and section bas as an alternative to welding processes
In this article we deal with the subject of tube bending as an alternative to welding. Welding is a procedure that is traditionally considered a carpentry process. It is often indispensable in processing tubes, but unfortunately it is also very expensive. What makes the procedure so costly is above all the need for constant controls to check correct performance. Thanks to the tube bending process, however, the need for welding can be eliminated – or greatly reduced, with enormous savings of time and production costs.
At the end of the Fifties, the first manufacturers of tube bending machines began to appear in Italy. However, although companies specialized in processing metal tubes have existed for over sixty years, an increase in the demand for bent steel tubes would develop only in the last twenty years.
The main factor that made this growth possible was unquestionably the increase in the production capacity of companies specialized in tube bending, like Tecnocurve, for example. There are at least four elements contributing to this increase in production capacity:
- the higher quality of bending thanks to the introduction of “FULL ELECTRIC” CNC machinery
- improvement in the esthetic appearance of the bent tube produced by this machinery
- an increase in the spread of know-how, also thanks to digital channels
- the possibility to reduce production costs.
Steel tube welding
The welding process for steel tubes and section bars is a joining practice known since the Middle Ages, consisting of joining two metal parts of the steel pipe by melting or inserting other material that, when melted near the sides to be joined, will create a permanent seam.
Welding can be used in almost every sector that requires joining metal tubes. In most cases it is unthinkable to replace welding with any other process. The downside to obtain a perfect welding process that lasts a long time is that many factors can affect it negatively. Just to mention a few:
- The welding procedure
- The design of the joint
- The cleanliness of the joint
- The presence of cracks
- The choice of filler material
- Defective weld seam
- Protection from rust
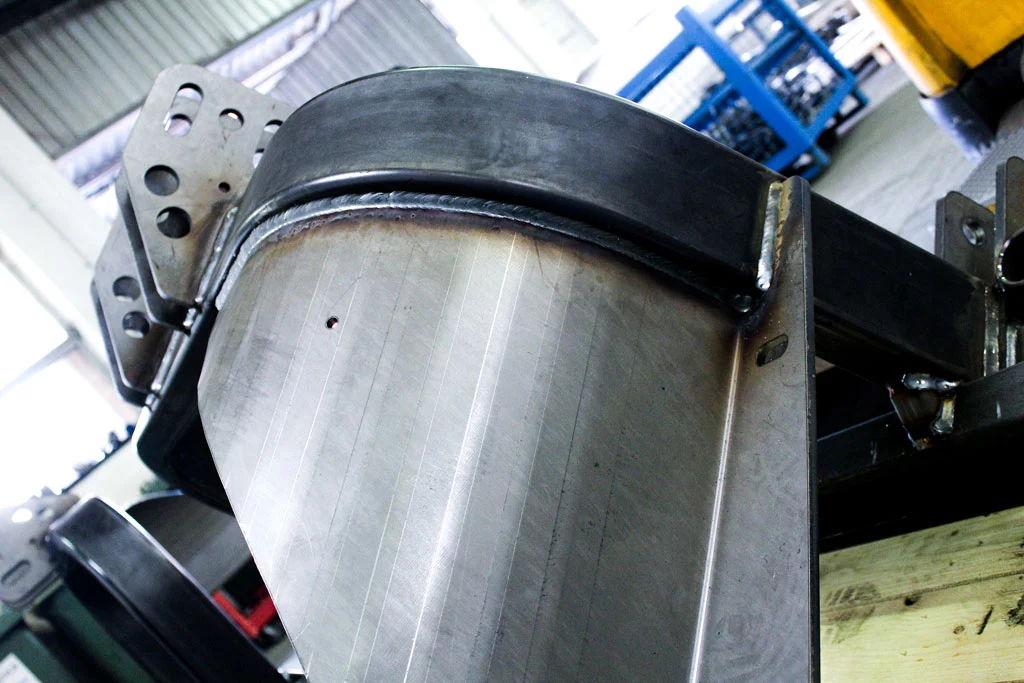
When tube bending replaces welding
In consideration of the risks listed above, it was necessary to find a solution that could reduce the risk factors connected with tube welding. This would enable us to speed up the production process on the one hand, and to reduce production costs on the other.
The solution consists of replacing welding on steel tubes with bending and roll- bending. This replacement is also possible for aluminum tubes and alloys, in which Tecnocurve has specialized over the years, particularly in the automotive, naval equipment, urban transport vehicles and cab machinery in general.
Bending and roll bending are processes whereby CNC tube bending machines (first case) or roll-bending equipment (second case) can be used to either bend the tubes around a matrix or pass them through a set of three rollers.
These processes give the tube its contour.
In addition to an initial study on the quality of the material and on the radius of the bend that can be achieved, the only other controls necessary on a bent tube concern the quality of the bend and the dimensional aspect (this latter is also necessary in case of welding). The controls serve to verify the correspondence of the bend with the customer’s specifications.
Another peculiarity in favor of the use of bending rather than welding for the tube, is the alteration to the mechanical characteristics of the metal caused by this latter process. While in bending the tubes, their characteristics are unaffected, since the process of shaping the tube is done “cold”, welding causes an increase in the temperature necessary to melt the metal, which alters its mechanical characteristics. Consequently, welded tubes are more inclined to break than bent tubes. This is especially true when the welding has not been done in a workmanlike manner.
A concrete example (and a satisfied customer)
The following is a concrete example of a case in which bending enabled our customer, specialized in the construction of industrial systems for the food sector, to reduce the number of processes, the costs of production and the production controls.
Initially, the customer would first cut the tubes with a laser and then weld them to form a single piece (first picture). Thanks to our process, the pipe is neither cut nor welded, but simply bent (second picture).
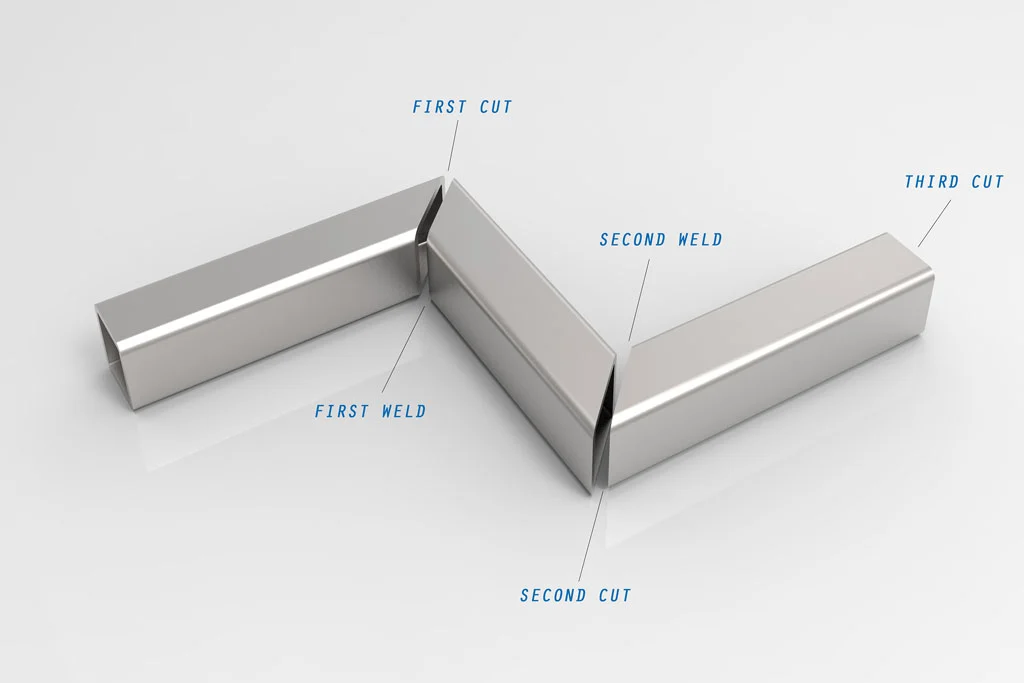
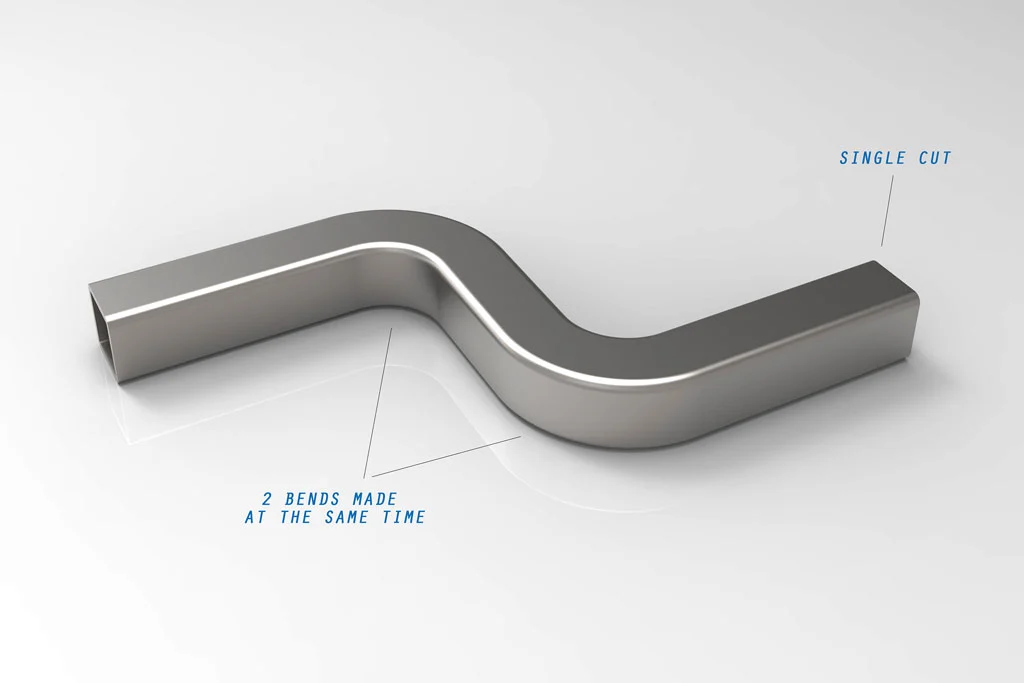
The reduction of the cuts by laser also meant a noticeable reduction in production timing and, consequently, in the costs. Performing two workmanlike welds (free of cracks, watertight, clean) is much more costly then equipping a CNC tube-bender.
This is true above all when there is a large number of pieces to be processed. Another aspect to consider is the esthetic aspect of the tube, which is certainly much better in the bent tube compared to the welded tube. The use of bending in place of welding makes it possible to introduce innovative solutions in all the processes involving bent tubes in view. In these cases, the tube becomes a real element of design, as typically happens with aluminum tubes in the sector of urban furnishing.
However, it is not always possible to eliminate welding completely. It will be necessary, in any case, after bending, to join the tube to all those parts (bushings, plates or other tubes) that form the finished product.
Conclusions
As we have seen, bending can, in some case, take the place of welding processes. However it is important to assess, case by case, all the aspects that involve metal tube processing. This will certainly also include:
- The quantity of tubes to bend or weld
- The importance of the esthetic aspect
- Whether or not a watertight seal is necessary (a welded tube always risks developing cracks in time; a bent tube would solve that problem)
- Various project assessments by the customer.
To facilitate the production process for the customer, Tecnocurve can count on the services of an advanced welding department capable of performing this work exactly on the materials that are bent, such as steel, stainless steel and aluminum.
The main welding methods used, qualified by specific certificates, are:
- Wire welding
- TIG welding.