In the late 1980s, Luciano Fadini, the visionary founder of Tecnocurve, recognised the revolutionary potential of cold bending of tubes, in particular steel tubes, and foresaw that it would become a fundamental industrial technology in the near future.
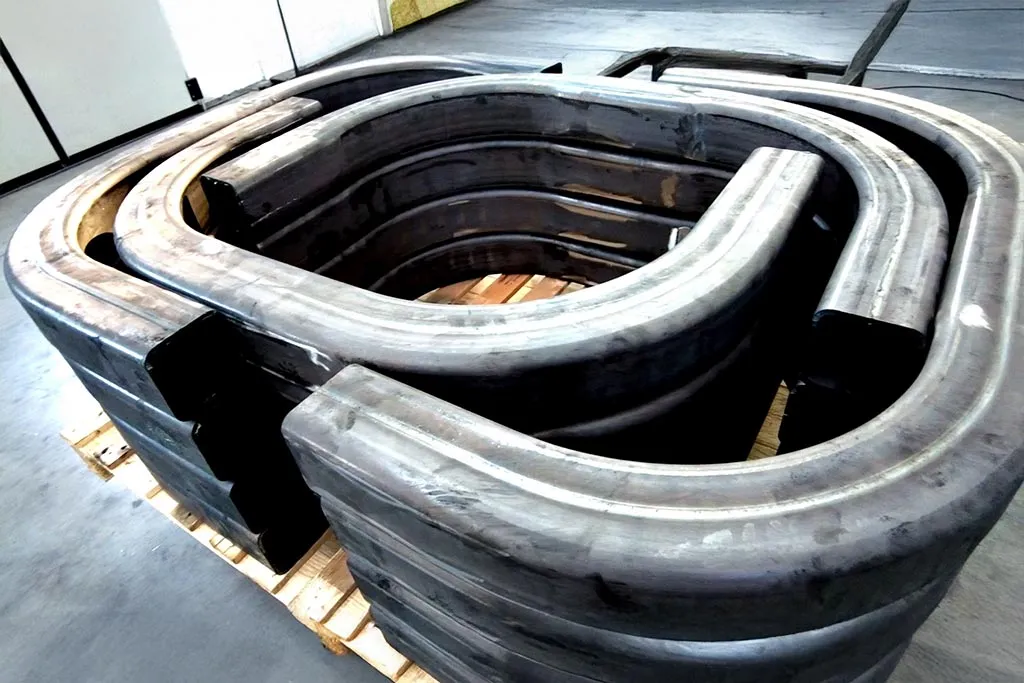
Tecnocurve was born out of this innovative vision and a deep passion for bending tubes and metal profiles.
The beginning of the activity in the 90s
The company started its activity in 1991 in a small industrial hall of 500 m², which was equipped with the first rolling and bending machines.
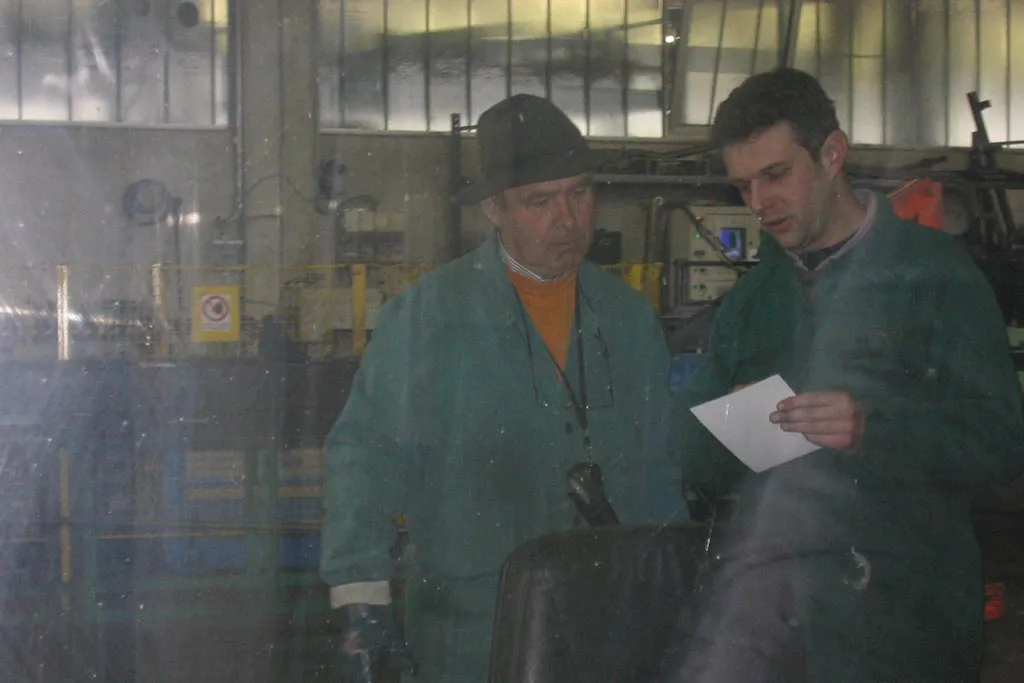
During this period, the agricultural machinery sector experienced exponential growth and Tecnocurve distinguished itself for its ability to meet the specific needs of agricultural machinery manufacturers who required bent tubular components.
There are numerous industrial applications, including three-point linkages (made of bent tubes with a square or rectangular cross-section), which are still important components in the manufacture of forage harvesters, vineyard machinery and lawnmowers.
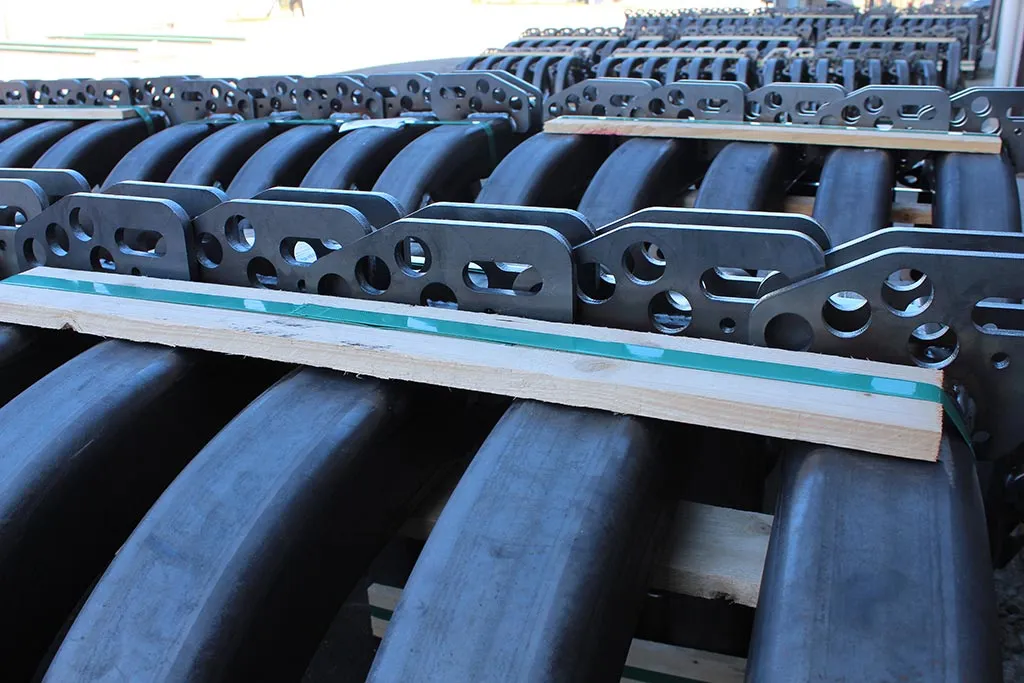
The ability to produce precise and standardised bends in large series using state-of-the-art machinery enables the company to guarantee its customers the highest quality standards and thus to stand out clearly from the competition.
The market for this innovative tube and profile bending and rolling technology is constantly growing and is also being used in other industries besides agriculture. Important partnerships are emerging in the production of steel and stainless steel pipe serpentines for the energy sector and special pipes for the construction of trams, railway carriages and buses.
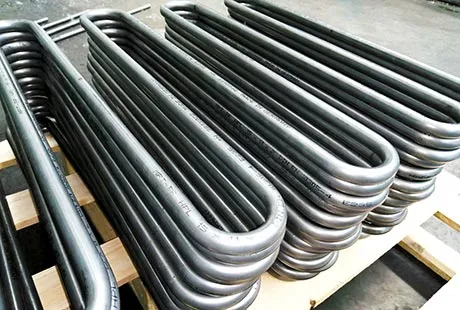
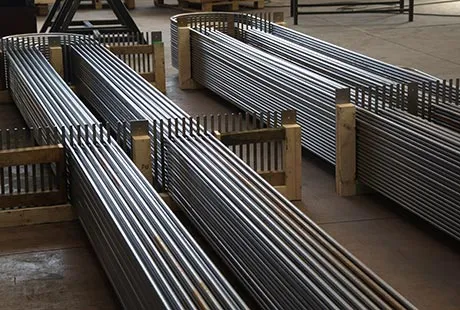
The company’s rapid expansion necessitated an initial 800 square metre extension to the factory in 1996. This expansion required the purchase of new state-of-the-art tube bending machines and the installation of new tube processing equipment, including semi-automatic circular saws and tube processing machines.
Expansion of machinery and introduction of quality management system
In 2001, certification of the quality management system became essential to guarantee and maintain high standards of performance for our customers, leading to the achievement and maintenance of ISO 9001 certification.
A decisive turning point occurred in 2004, when, in order to maintain its technological leadership, one of the most innovative tube bending machines on the market was purchased, capable of bending tubes with the following cross-sections:
- Ø139.7 mm for round tubes
- 120×120 mm for square tubes
Between 2006 and 2009, a further significant expansion of 1500 square metres was realised.
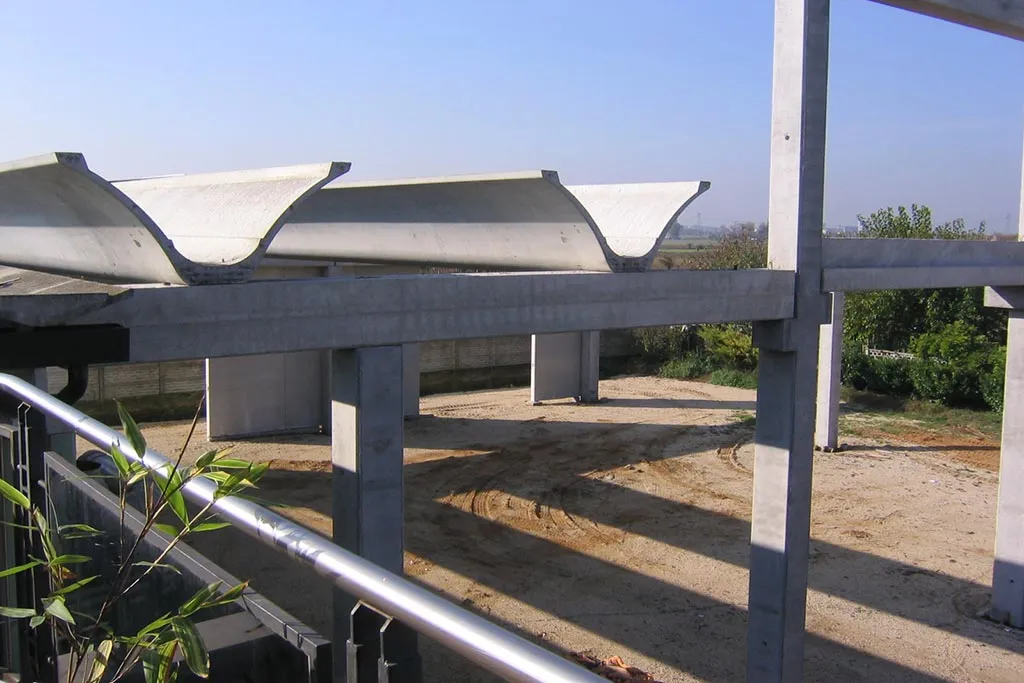
At the same time, the company began attending the most important international agricultural exhibitions (such as the prestigious SIMA in Paris).
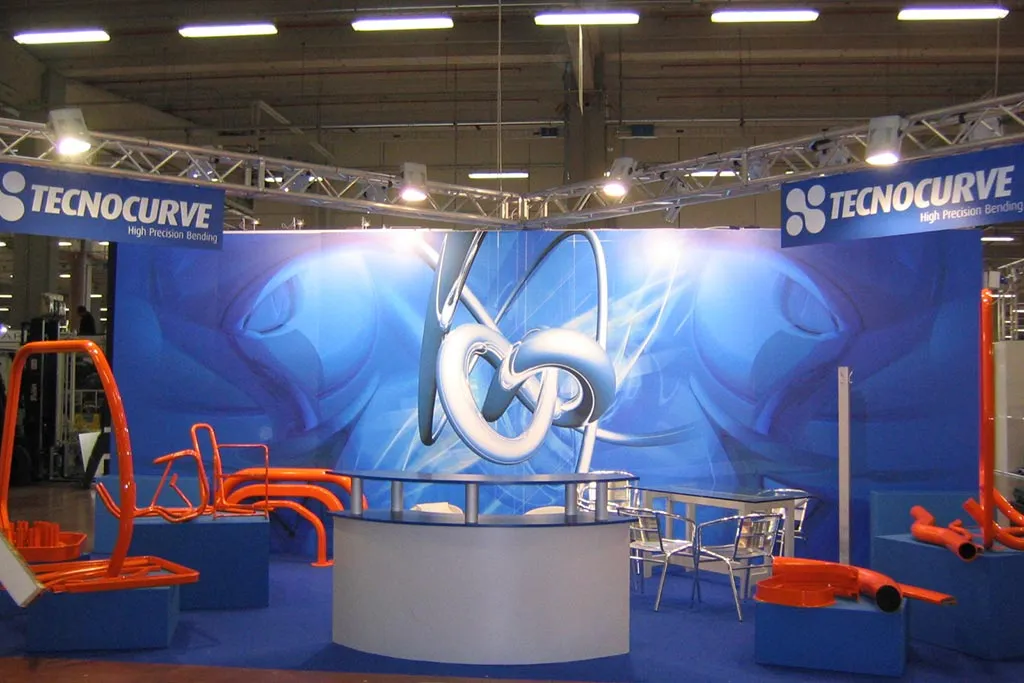
Participation in international trade fairs
Participation in international trade fairs enabled Tecnocurve to acquire strategic customers abroad and to establish partnerships with important French multinationals in the agricultural industry, with which the company still maintains close supplier relationships.
In addition to the processing of round, square and rectangular tubes, Tecnocurve stands out for its precision bending of tubes and pipes, which are used strategically in certain areas such as the construction of cabins and lighting. In the context of cabins: the shape of these profiles, which differs from that of standard tubes and pipes, guarantees:
- a better appearance
- the possibility of integrating glass on one side and the supporting structure on the other
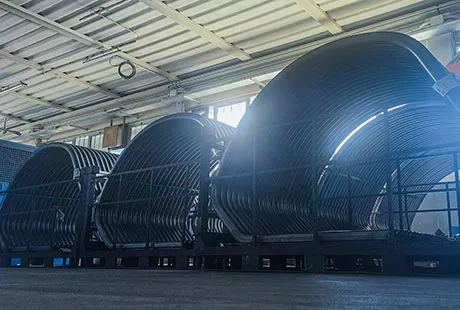
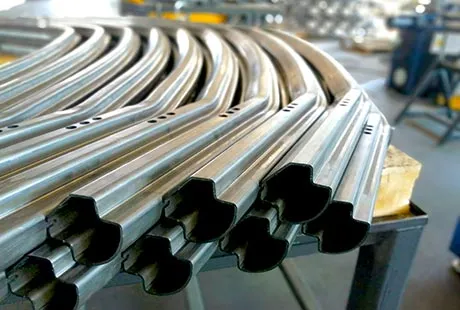
A fundamental innovation for the company’s growth was the introduction of the first laser tube, which, in combination with roll bending, makes it possible to carry out several processes on a straight tube, optimising production times and costs. The following series of processes are possible:
- precision drilling
- technical slots
- angle cuts
- specialised chamfering
- professional tube bevelling
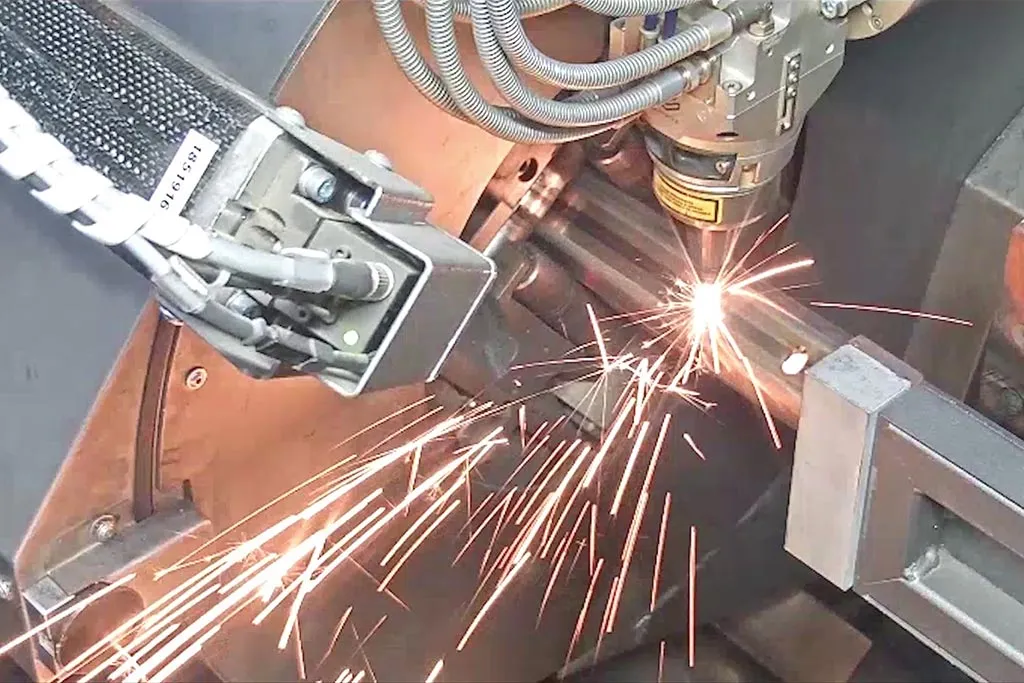
In 2014, the company significantly expanded its machine park, in particular with a tube bending machine using FULL ELECTRIC technology, which guarantees higher precision and the possibility of serial production of bent tubes.
A new phase of expansion since 2016
Since 2016, a new phase of expansion has begun, characterised by the acquisition of state-of-the-art machinery and new processing options to offer customers complete solutions:
- Specialised department for welding pipes
- Two advanced CNC milling centres
- Latest-generation CNC lathe
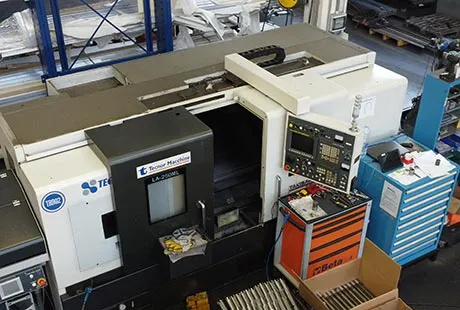
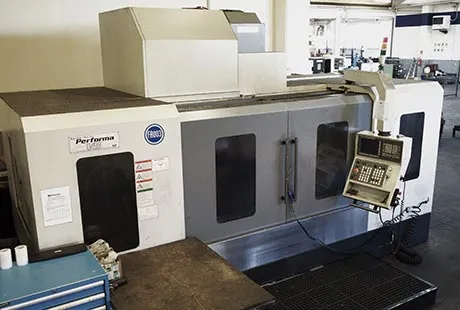
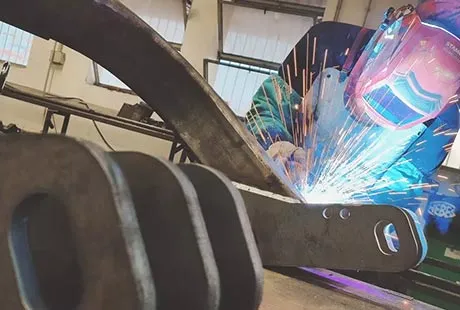
In 2018, the company expanded its production area by a further 3,000 m² and invested in a second laser cutting system for tubes to meet growing market demand.
Between 2013 and 2018, Tecnocurve has seen a strong growth in its workforce, from 25 to around 70 qualified employees.
A decisive moment was the purchase of one of the most advanced tube bending machines on the market: the Crippa 225 Full Electric. This state-of-the-art machine can bend metal tubes up to 219 mm in diameter for round tubes and square sections up to 180×180 mm.
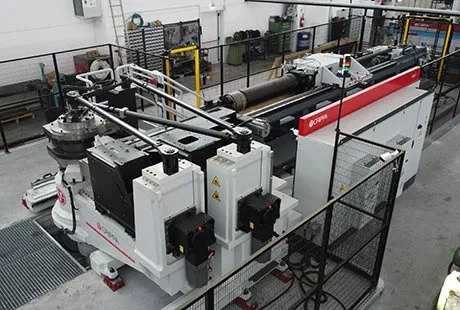
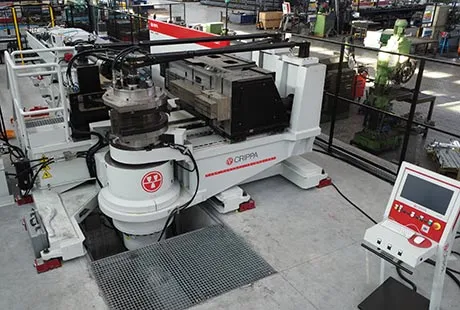
In 2020, we obtain the UNI EN 1090 certification, an international recognition that certifies the quality of our production processes for carbon steel components.
In 2023, the last expansion will be completed: our industrial hall will reach a total area of 10,000 square metres, divided into a state-of-the-art production area, a modern office area and a warehouse.
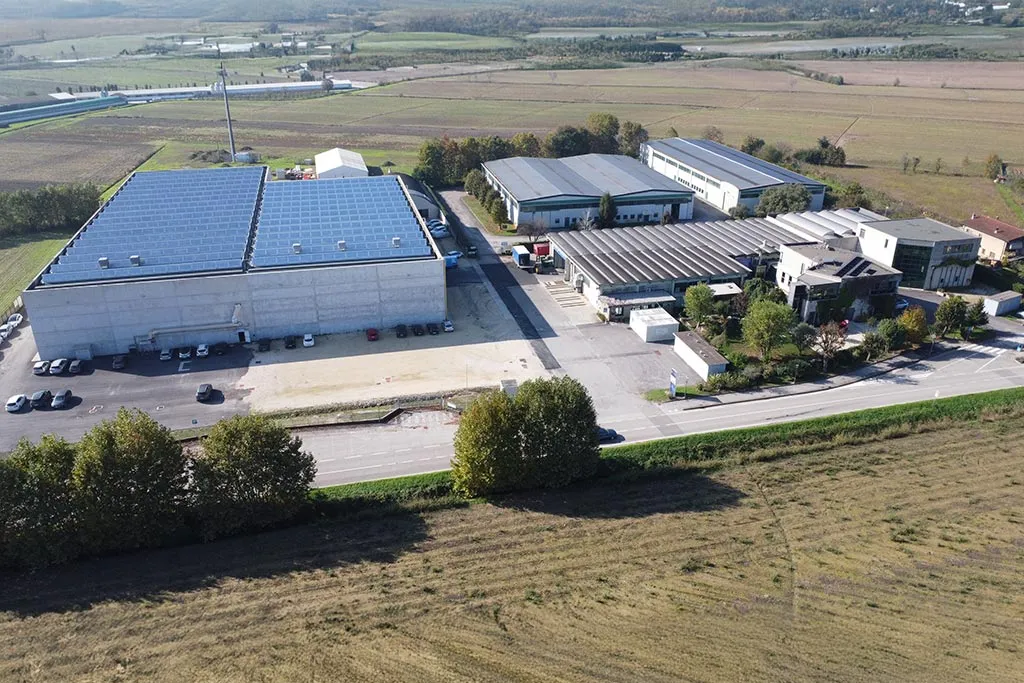
Our presence at the most important international trade fairs in the metal industry continues to be of fundamental importance for the growth of our company. We regularly take part in the following trade fairs:
- EIMA in Bologna
- AGRITECHNICA in Hannover
- HANNOVERMESSE in Hannover
- TUBE in Düsseldorf
We look forward to seeing you at our stand!
For more than three decades, we have been bending tubes. During this time, we have perfected our technical expertise and our production capacities to meet the growing demands of our customers, who now come from all over the world and from a wide range of industries:
Many chapters of our history have already been written, and many more are yet to come. We are always looking ahead, towards a future of continuous technological and productive evolution. Our primary objective, past, present and future, remains the same: to continue to improve our position in the global tube processing market.